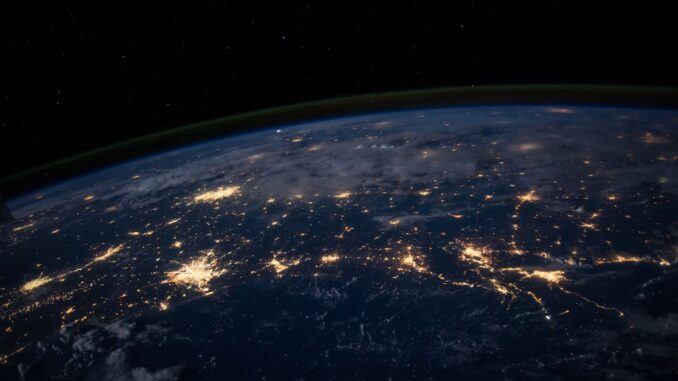
Abstract
Digital twin technology, a sophisticated paradigm involving the creation of dynamic, virtual replicas of physical assets, systems, or processes, has emerged as a profoundly transformative tool across an extensive spectrum of industries. This comprehensive research report undertakes an in-depth exploration of the multifaceted applications of digital twins, dissecting their pivotal role in enhancing operational efficiency, fostering innovation, and enabling data-driven decision-making. It meticulously examines the intricate technological infrastructure required for their development and sustainment, encompassing advancements in areas such as the Internet of Things (IoT), artificial intelligence (AI), machine learning (ML), cloud and edge computing, and high-performance computing. Furthermore, the report critically analyzes the significant challenges associated with their implementation, maintenance, and ethical governance. By scrutinizing diverse industry applications, ranging from the granular optimization of manufacturing processes to the macro-level planning of smart urban environments, and by delving into the synergistic integration of advanced computational methodologies, this report provides a thorough and nuanced understanding of digital twin technology’s current landscape, its burgeoning potential, and the strategic pathways for its future evolution.
Many thanks to our sponsor Esdebe who helped us prepare this research report.
1. Introduction
The conceptual genesis of a digital twin—a precise, dynamic, and virtual representation of a physical object, system, or even an entire environment—can be traced back to early visionary ideas within NASA in the 1960s, where simulations of space capsules were crucial for understanding and mitigating potential failures during missions like Apollo 13. Dr. Michael Grieves, then a professor at the University of Michigan, formally introduced the concept as a ‘Mirrored Spaces Model’ in 2002, laying the theoretical groundwork for what we now understand as the digital twin. This foundational concept posited a lifecycle management system for products, connecting a physical product with its virtual counterpart, facilitating data exchange and operational insights throughout its existence. While initially conceptualized within the aerospace domain, the digital twin has, in recent years, gained unprecedented traction across a myriad of sectors, evolving from a theoretical construct into a versatile and indispensable tool utilized to dramatically enhance operational efficiency, spur unprecedented innovation, and fundamentally reshape decision-making processes (en.wikipedia.org).
At its core, a digital twin is more than just a 3D model or a simulation. It is a live, constantly evolving virtual model that is continuously updated with real-time data from its physical counterpart via sensors, IoT devices, and other data sources. This bi-directional data flow is crucial: data from the physical asset feeds the digital twin, allowing it to accurately reflect the physical state, behavior, and environment. Conversely, insights derived from the digital twin, through analysis, simulation, and predictive modeling, can be used to inform, optimize, and even control the physical asset. This dynamic linkage enables continuous monitoring, performance optimization, predictive maintenance, and scenario planning in a risk-free virtual environment before actions are taken in the physical world.
The profound significance of digital twin technology lies in its capacity to bridge the chasm between the physical and digital realms. It creates a robust framework for understanding complex systems, anticipating outcomes, and making proactive, data-driven decisions. Unlike static models or simulations that represent a snapshot in time or a predefined set of conditions, a digital twin provides a persistent, living representation that evolves with its physical twin. This dynamic fidelity allows organizations to gain unparalleled insights into the performance, health, and potential future states of their assets, leading to optimized resource utilization, reduced downtime, enhanced safety, and accelerated innovation cycles. The integration of advanced technologies, which will be elaborated upon in subsequent sections, amplifies the power of digital twins, positioning them as a cornerstone of Industry 4.0 and a catalyst for future technological advancements.
Many thanks to our sponsor Esdebe who helped us prepare this research report.
2. Applications of Digital Twin Technology
The transformative potential of digital twin technology is evidenced by its widespread and growing adoption across a diverse array of industries, each leveraging its unique capabilities to address specific challenges and unlock new opportunities. The following sections detail prominent applications:
2.1 Manufacturing Industry
In the manufacturing sector, digital twins are revolutionizing every stage of the product lifecycle, from initial design and prototyping to production, operations, and maintenance. They serve as virtual prototypes, enabling companies to meticulously simulate and optimize entire production processes, individual machinery performance, and even factory layouts before any physical capital is committed. This virtual testing environment significantly reduces costs, accelerates time-to-market, and minimizes errors inherent in traditional trial-and-error approaches.
For instance, Siemens, a global powerhouse in industrial automation, extensively employs digital twin technology to optimize the maintenance and operational efficiency of complex assets like their industrial gas turbines. By creating a digital replica of each turbine, continuously fed with real-time data on temperature, pressure, vibration, and performance metrics, Siemens can predict potential failures with high accuracy, often weeks or months in advance. This capability allows for the proactive scheduling of maintenance activities during planned downtimes, thereby avoiding catastrophic failures, reducing unplanned downtime by up to 30%, and significantly extending the lifespan of critical machinery (datanext.ai). Beyond individual assets, digital twins are also used to model entire production lines, optimizing material flow, bottleneck identification, and quality control processes. This extends to supply chain optimization, where a digital twin of the supply network can simulate disruptions, evaluate alternative routes, and forecast demand fluctuations, ensuring resilience and efficiency.
2.2 Healthcare Sector
The healthcare industry stands on the cusp of a profound transformation, with digital twins poised to personalize medicine, enhance surgical precision, and streamline hospital operations. The creation of ‘digital patient’ models is a particularly groundbreaking application, enabling healthcare professionals to tailor treatment plans with unprecedented accuracy.
Philips, a leader in health technology, has been at the forefront of developing such ‘digital patient’ models. These sophisticated twins integrate a patient’s unique physiological data—including genetic information, medical history, real-time vital signs from wearable devices, imaging scans (CT, MRI), and even lifestyle data—to create a dynamic, personalized representation. This allows clinicians to simulate the effects of different medications, predict disease progression, and virtually ‘rehearse’ complex surgical procedures. For instance, a digital twin of a patient’s heart can be used to simulate blood flow dynamics, predict the efficacy of various stent placements, or even pre-plan intricate cardiac surgeries, thereby minimizing risks, improving patient outcomes, and significantly reducing the need for invasive diagnostic procedures (hologram.io). Furthermore, digital twins are being explored for drug discovery, simulating molecular interactions and drug efficacy in a virtual environment, thereby accelerating research and reducing the reliance on costly animal testing. Beyond individual patients, digital twins of hospitals can optimize patient flow, resource allocation (beds, staff, equipment), and emergency response planning, leading to more efficient and responsive healthcare systems.
2.3 Urban Planning and Smart Cities
Urban planners and municipal authorities are increasingly leveraging digital twin technology to model entire cities, providing a comprehensive, real-time overview that aids in strategic infrastructure development, dynamic traffic management, environmental monitoring, and disaster preparedness. These city-level digital twins, often referred to as ‘urban twins’ or ‘city information models,’ integrate vast datasets from diverse sources, including geospatial data, building information models (BIM), IoT sensors (for traffic, air quality, noise), public transport data, and demographic information.
Singapore, a recognized pioneer in smart city initiatives, has developed a highly advanced digital twin known as ‘Virtual Singapore.’ This comprehensive 3D semantic model of the entire city-state serves as a collaborative platform for various stakeholders, including government agencies, businesses, and researchers. It allows for the simulation of complex urban phenomena, such as the impact of rising sea levels on coastal infrastructure, the optimization of public transportation routes to alleviate congestion, the assessment of urban heat island effects, and the strategic placement of new public amenities (hologram.io). By enabling ‘what-if’ scenario planning, city digital twins facilitate more informed policy-making, resource allocation, and sustainable urban development, ultimately enhancing the quality of life for residents and improving urban resilience in the face of environmental and societal challenges.
2.4 Energy and Utilities
The energy and utilities sector, characterized by vast, complex, and geographically dispersed infrastructure, is a prime candidate for digital twin adoption. Digital twins are instrumental in monitoring, optimizing, and managing the performance of power grids, renewable energy sources, oil and gas facilities, and water distribution networks. They enable real-time analysis, predictive maintenance, and enhanced operational control.
In the realm of renewable energy, digital twins of wind farms or solar arrays can integrate data from thousands of sensors on individual turbines or panels, monitoring factors like wind speed, solar irradiance, temperature, and vibration. This allows operators to precisely track energy generation, predict maintenance needs for individual components, and optimize the overall output of the entire farm. For instance, a digital twin can identify a specific wind turbine blade experiencing unusual vibrations, allowing for pre-emptive repair before a critical failure occurs. In traditional power grids, digital twins enhance grid stability and resilience by simulating load fluctuations, predicting outages, and optimizing power distribution, leading to enhanced efficiency and reduced downtime across the network (marketsandmarkets.com). For critical infrastructure like nuclear power plants, digital twins provide a safe virtual environment for simulating complex operational procedures, emergency responses, and predictive degradation analysis, thereby enhancing safety and regulatory compliance.
2.5 Aerospace and Defense
The aerospace and defense industry has been an early adopter and continues to be a significant beneficiary of digital twin technology. From aircraft design and manufacturing to in-service monitoring and maintenance, digital twins provide unparalleled insights.
For an aircraft manufacturer, a digital twin can represent a single component, an entire engine, or even a complete aircraft. During design, engineers can use the twin to simulate aerodynamic performance, structural integrity under various loads, and thermal management, significantly reducing the need for costly physical prototypes and lengthy test cycles. Once an aircraft is in service, its digital twin is continuously updated with flight data, sensor readings from engines, airframes, and systems. This real-time data allows for precise health monitoring, predicting the remaining useful life of components, and scheduling proactive maintenance. For example, Rolls-Royce utilizes digital twins for their jet engines, enabling airlines to optimize fuel consumption, extend engine lifespan, and minimize unscheduled maintenance. In defense, digital twins are used for optimizing weapon systems, training simulations for personnel, and managing complex battlefield assets, enhancing operational readiness and tactical decision-making.
2.6 Automotive Industry
The automotive sector is rapidly embracing digital twins across vehicle design, manufacturing, and the entire vehicle lifecycle, particularly with the advent of electric and autonomous vehicles.
Digital twins are fundamental in the development of new car models, allowing engineers to simulate crash tests, aerodynamic performance, and thermal management in a virtual environment, significantly reducing prototyping costs and time. For electric vehicles, digital twins of battery packs monitor cell health, charge cycles, and degradation over time, optimizing performance and predicting battery lifespan. Perhaps most critically, digital twins are indispensable for testing and validating autonomous driving systems. A virtual replica of a car, its sensors (cameras, radar, lidar), and its environment (roads, traffic, pedestrians, weather conditions) allows millions of miles of driving scenarios to be simulated safely and efficiently, evaluating the performance of AI algorithms and ensuring the safety of self-driving cars before they ever hit the road (time.com). Furthermore, digital twins enable predictive maintenance for individual vehicles, informing owners when specific components require attention based on their driving style and vehicle sensor data.
2.7 Retail and Consumer Goods
While seemingly less complex than industrial applications, digital twins are finding innovative uses in retail and consumer goods to optimize operations, enhance customer experience, and improve supply chain efficiency.
In retail, a digital twin of a store layout can be created to simulate customer flow, product placement effectiveness, and queue management, allowing retailers to optimize store design for maximum sales and customer satisfaction. Supply chain digital twins allow for real-time monitoring of goods movement, inventory levels across warehouses, and potential disruptions (e.g., weather events, port congestion). This enables agile responses, optimized stock levels, and reduced logistics costs. For consumer goods manufacturing, digital twins of production lines can simulate new product introductions, assess the impact of changes on efficiency, and ensure consistent product quality across distributed manufacturing sites.
Many thanks to our sponsor Esdebe who helped us prepare this research report.
3. Technological Requirements for Developing Digital Twins
The effective development and deployment of digital twin technology necessitate a robust and integrated technological ecosystem. These requirements extend beyond simple software and hardware to encompass sophisticated data acquisition, processing, analytical, and visualization capabilities. The synergy between these technologies is what empowers a digital twin to be a dynamic, insightful, and actionable virtual representation.
3.1 Internet of Things (IoT)
The Internet of Things forms the sensory backbone of any digital twin implementation. IoT devices are integral, providing the indispensable real-time data streams from physical assets, environments, and even human interactions that fuel the digital twin. Without this constant influx of current data, a digital twin would merely be a static model or a simulation, lacking the dynamic fidelity that defines its true value.
Sensors are the primary data collection agents, encompassing a vast array of types: accelerometers detect vibration and movement; temperature sensors monitor thermal conditions; pressure sensors gauge force and flow; proximity sensors detect presence; acoustic sensors capture sound signatures; and cameras provide visual data. Beyond direct sensing, RFID tags, GPS modules, and other telemetry devices contribute location, identification, and operational data. These IoT components are embedded within, or attached to, physical assets and infrastructure, continuously collecting and transmitting raw data—often in massive volumes—which forms the foundational input for the digital twin models. The reliability, accuracy, and latency of this data transfer are paramount, demanding robust network connectivity (such as 5G, Wi-Fi 6, or Low-Power Wide-Area Networks like LoRaWAN) and secure communication protocols to ensure data integrity and real-time synchronization (iml.fraunhofer.de).
3.2 Cloud Computing and Edge Computing
The immense volume, velocity, and variety of data generated by IoT devices necessitate a powerful and flexible computing infrastructure. This requirement is typically addressed through a synergistic combination of cloud computing and edge computing paradigms.
Cloud Computing offers unparalleled scalability, vast storage capabilities, and extensive processing power, making it ideal for hosting the digital twin model itself, performing complex analytics, and storing historical data. Cloud platforms provide on-demand resources, allowing organizations to scale their digital twin infrastructure as their needs evolve, without significant upfront capital investment. They enable global accessibility for distributed teams and facilitate the integration of diverse data sources from multiple assets or locations. The benefits include cost-effectiveness, high availability, disaster recovery, and access to a broad ecosystem of development tools and AI/ML services.
Edge Computing, conversely, facilitates real-time data processing closer to the source—at the ‘edge’ of the network, often directly on the IoT devices or local gateways. This localized processing significantly reduces latency, which is critical for applications requiring immediate responses, such as real-time control of machinery or rapid anomaly detection. By pre-processing and filtering data at the edge, the volume of data transmitted to the cloud is reduced, conserving bandwidth and mitigating privacy concerns for sensitive data. A hybrid architecture, where critical real-time operations are handled at the edge and more complex analytics, long-term storage, and overarching model updates occur in the cloud, represents a common and highly effective deployment strategy for comprehensive digital twin solutions (iml.fraunhofer.de).
3.3 Artificial Intelligence and Machine Learning
Artificial Intelligence (AI) and Machine Learning (ML) algorithms are the intelligent core of digital twin technology, transforming raw data into actionable insights and enabling predictive capabilities. These technologies analyze the voluminous data collected by IoT devices, identifying patterns, correlations, and anomalies that human operators might miss.
AI and ML empower digital twins to perform advanced functions such as:
* Predictive Analytics: Forecasting future states of the physical asset, such as predicting equipment failure (e.g., Remaining Useful Life – RUL estimation), energy consumption patterns, or material degradation. Techniques like regression analysis, time-series forecasting, and deep learning models are commonly employed.
* Anomaly Detection: Identifying unusual behavior or deviations from normal operating parameters that could indicate an impending issue or a security breach. Unsupervised learning algorithms, such as clustering and autoencoders, are often used here.
* Optimization: Recommending optimal operational parameters to maximize efficiency, minimize energy consumption, or improve product quality. Reinforcement learning, for example, can be used to teach a digital twin to make optimal decisions in complex environments.
* Diagnostic Capabilities: Pinpointing the root cause of an issue once an anomaly is detected, based on historical data and expert knowledge. Rule-based systems and classification algorithms contribute here.
* Autonomous Decision-Making: In advanced applications, AI can enable the digital twin to make autonomous adjustments to the physical asset based on real-time analysis and predicted outcomes, within predefined safety parameters. This is crucial for self-optimizing systems in manufacturing or smart city traffic management.
The continuous learning capability of ML algorithms allows the digital twin to become progressively more accurate and insightful over time as it processes more data and encounters new scenarios (iml.fraunhofer.de).
3.4 Supercomputing and High-Performance Computing (HPC)
For exceptionally complex simulations and the modeling of large-scale, intricate systems, traditional computing infrastructure may fall short. This is where supercomputing and High-Performance Computing (HPC) resources become indispensable.
Supercomputers, with their massive parallel processing capabilities, are essential for running multi-physics simulations that involve complex interactions across various domains (e.g., fluid dynamics, thermal dynamics, structural mechanics) simultaneously. Examples include modeling global oceanic systems for climate research, simulating the behavior of entire city ecosystems, or designing advanced materials at the atomic level. These high-fidelity simulations generate enormous datasets and require immense computational power to process within reasonable timeframes, providing granular insights into intricate systems and phenomena that would be impossible to analyze with standard computing resources (itpro.com). HPC also plays a crucial role in training large, complex AI models that underpin the predictive and analytical capabilities of advanced digital twins, especially those deployed in fields like aerospace, automotive R&D, and pharmaceutical discovery.
3.5 3D Modeling, Simulation, and Visualization Software
While data forms the core, the ability to represent and interact with the digital twin visually is paramount for human understanding and intervention. This requires sophisticated 3D modeling, simulation, and visualization software.
- Computer-Aided Design (CAD) and Building Information Modeling (BIM) tools are used to create the initial geometric and semantic models of the physical asset. These models provide the fundamental structure and properties of the twin.
- Computer-Aided Engineering (CAE) tools, including Finite Element Analysis (FEA) and Computational Fluid Dynamics (CFD), enable the simulation of physical behaviors, stress analysis, fluid flow, and thermal performance, providing critical insights into the asset’s performance under various conditions.
- Simulation Platforms integrate these models with real-time data, allowing for dynamic testing of scenarios, ‘what-if’ analysis, and the prediction of outcomes. These platforms often incorporate physics-based engines to accurately mimic real-world phenomena.
- Visualization Tools provide intuitive graphical user interfaces (GUIs), dashboards, augmented reality (AR), and virtual reality (VR) environments to enable users to interact with the digital twin. This interaction can range from simple data display to immersive walkthroughs of a virtual factory, enabling remote diagnostics, training, and collaborative problem-solving.
3.6 Data Analytics and Integration Platforms
Beyond raw data collection, sophisticated platforms are required to ingest, store, process, and analyze the diverse data streams feeding the digital twin. This involves data lakes or data warehouses, streaming analytics engines, and robust data integration tools. These platforms ensure data quality, consistency, and accessibility, transforming disparate data points into a unified, coherent information model suitable for AI/ML processing and visualization. Data governance strategies are also crucial to manage data lineage, access controls, and compliance across the entire data lifecycle.
Many thanks to our sponsor Esdebe who helped us prepare this research report.
4. Benefits of Digital Twin Technology
Adopting digital twin technology yields a multitude of strategic and operational benefits, fundamentally transforming how organizations design, operate, and maintain their assets and systems. These advantages translate directly into enhanced efficiency, reduced costs, accelerated innovation, and improved decision-making across the board.
4.1 Enhanced Decision-Making
Digital twins provide a rich, accurate, and real-time data-driven foundation for informed decision-making at all levels of an organization—strategic, tactical, and operational. By integrating diverse data streams from the physical world and applying advanced analytical models, digital twins offer a holistic and current view of an asset’s or system’s state, performance, and potential future behavior.
Unlike traditional reporting, which often relies on historical data, digital twins provide predictive insights, allowing decision-makers to anticipate challenges and opportunities before they materialize. For example, in urban planning, a city’s digital twin can simulate the impact of new zoning laws on traffic congestion or energy consumption, enabling policymakers to make proactive adjustments. In manufacturing, a digital twin of a production line can model the impact of different scheduling strategies on throughput, guiding managers to optimal solutions. This capability significantly mitigates risks by allowing for ‘what-if’ scenario analysis in a virtual environment, testing various hypotheses and evaluating potential outcomes without incurring real-world costs or disruptions (marketsandmarkets.com). The ability to visualize complex data and simulate future scenarios empowers leaders to make more strategic, data-backed decisions, moving from reactive problem-solving to proactive optimization.
4.2 Improved Operational Efficiency
One of the most immediate and tangible benefits of digital twin technology is the significant improvement in operational efficiency. By virtually simulating, analyzing, and optimizing processes, digital twins help organizations identify inefficiencies, pinpoint bottlenecks, and implement corrective measures, leading to substantial cost savings and increased productivity.
For instance, in a factory setting, a digital twin can model the flow of materials and products through the entire production line. This allows engineers to identify and eliminate wasted motion, optimize machinery utilization, balance workloads, and reduce energy consumption. By virtually testing modifications to the production process, companies can achieve higher throughput, lower operational expenses, and reduce waste without disrupting actual operations. Furthermore, real-time monitoring through the digital twin enables dynamic adjustments to operating parameters, ensuring that assets perform at their peak efficiency continuously. This granular level of insight and control leads to optimized resource allocation, minimized downtime, and ultimately, a more streamlined and productive operational environment (asme.org).
4.3 Predictive Maintenance
Digital twins revolutionize maintenance strategies by enabling a shift from reactive or time-based maintenance to highly efficient predictive maintenance. By continuously monitoring the condition of assets through real-time sensor data and applying advanced analytics, digital twins can predict potential failures or performance degradations before they occur.
This capability allows organizations to schedule maintenance activities precisely when needed, rather than performing unnecessary maintenance too frequently or suffering costly downtime due to unexpected breakdowns. The digital twin can analyze vibration patterns, temperature fluctuations, pressure changes, and other operational parameters to detect subtle anomalies indicative of impending failure. It can then alert maintenance teams, providing insights into the specific component at risk and its estimated Remaining Useful Life (RUL). This proactive approach significantly reduces unplanned downtime, extends the lifespan of machinery, optimizes the spare parts inventory, and dramatically lowers overall maintenance costs (marketsandmarkets.com). For critical assets, this translates directly to enhanced safety and reliability.
4.4 Innovation and Product Development
The ability to test and iterate designs virtually within a digital twin environment significantly accelerates product development cycles and fosters unprecedented innovation. This benefit is particularly pronounced in industries with complex products and long development timelines.
Digital twins enable rapid prototyping and virtual testing of new designs, materials, and features. Engineers can create multiple virtual iterations of a product, subject them to various simulated conditions (e.g., stress, temperature extremes, operational loads), and evaluate their performance without the expense and time involved in building physical prototypes. For example, in the automotive industry, digital twins are extensively used to simulate and improve the safety of self-driving cars, testing millions of miles of scenarios, including challenging environmental conditions and unexpected events, long before physical vehicles are deployed (time.com). This virtual sandbox environment allows for continuous experimentation, encourages radical design changes, and facilitates co-creation among geographically dispersed teams, ultimately leading to faster time-to-market for new products, higher quality, and more innovative solutions that better meet market demands.
4.5 Risk Management and Safety
Digital twins provide a powerful platform for identifying, assessing, and mitigating risks across various operational contexts. By simulating hazardous scenarios or predicting potential failures, they significantly enhance safety protocols and emergency preparedness.
In high-risk environments like offshore oil rigs, nuclear power plants, or chemical facilities, a digital twin can simulate critical operational procedures, emergency shutdown sequences, and the impact of equipment failures. This allows operators to train in a risk-free virtual environment, identify potential vulnerabilities in existing systems, and develop more robust emergency response plans. For infrastructure like bridges or buildings, a digital twin can monitor structural health in real-time, detecting early signs of fatigue or damage and predicting potential collapse, thereby allowing for timely intervention and preventing catastrophic events. This proactive risk identification and mitigation capability not only protects human life but also safeguards valuable assets and reduces financial exposure.
4.6 Training and Education
Digital twins offer immersive and realistic training environments, enabling employees to gain practical experience without risking damage to expensive equipment or jeopardizing safety. This leads to more effective learning outcomes and reduces the reliance on physical resources.
Operators can interact with the digital twin of complex machinery, practice troubleshooting procedures, or simulate maintenance tasks, gaining hands-on experience in a safe, controlled virtual space. This is particularly valuable for training new employees, upskilling existing staff on new equipment, or preparing for rare but critical operational events. For example, airline pilots can train in sophisticated flight simulators, which are essentially digital twins of real aircraft, to practice emergency landings or navigate challenging weather conditions. This significantly improves skill retention, reduces training costs, and ensures that personnel are well-prepared for real-world scenarios, ultimately contributing to higher operational efficiency and safety standards.
Many thanks to our sponsor Esdebe who helped us prepare this research report.
5. Challenges in Developing and Maintaining Digital Twins
While the benefits of digital twin technology are compelling, its implementation and ongoing maintenance present a complex array of challenges that organizations must carefully address. These challenges span technical, organizational, financial, and ethical dimensions, requiring strategic planning and robust governance frameworks.
5.1 Data Security and Privacy
The integration of vast amounts of real-time operational data, often highly sensitive or proprietary, from numerous sources into a centralized digital twin model raises significant concerns regarding data security and privacy. The continuous flow of data from physical assets, combined with insights generated by the digital twin, creates potential vulnerabilities that malicious actors could exploit.
Ensuring robust cybersecurity measures is paramount. This includes implementing strong encryption for data in transit and at rest, establishing rigorous access control mechanisms, employing multi-factor authentication, and conducting regular vulnerability assessments and penetration testing. The risk of data breaches, intellectual property theft, and sabotage through compromising the digital twin is substantial. Furthermore, when digital twins involve personal or health-related data (as in healthcare applications), strict compliance with data protection regulations such as GDPR (General Data Protection Regulation), HIPAA (Health Insurance Portability and Accountability Act), and CCPA (California Consumer Privacy Act) is non-negotiable. Organizations must develop clear data governance policies that define data ownership, usage rights, retention periods, and anonymization procedures to safeguard privacy and maintain trust (reuters.com).
5.2 Integration Complexities
Integrating digital twins into existing IT and operational technology (OT) infrastructures can be an exceedingly complex undertaking. Most organizations operate with a heterogeneous landscape of legacy systems, disparate data sources, and proprietary platforms that were not initially designed for real-time data exchange or interoperability.
Challenges include:
* Legacy System Compatibility: Older systems may lack the necessary APIs or data formats to seamlessly connect with modern digital twin platforms, requiring significant effort in developing custom connectors or middleware.
* Data Silos: Information is often fragmented across various departments and systems, making it difficult to consolidate into a unified model for the digital twin.
* Standardization Deficiencies: A lack of industry-wide standards for data models, communication protocols, and interface specifications can hinder seamless integration across different vendors’ equipment and software.
* Network Infrastructure: Ensuring reliable, low-latency connectivity for massive IoT data streams can strain existing network capabilities, requiring upgrades to 5G, fiber optics, or dedicated industrial networks.
A well-thought-out integration strategy, involving phased deployment, robust API management, and a focus on open standards where possible, is essential for seamless and efficient integration (iml.fraunhofer.de).
5.3 Scalability and Flexibility
As organizations grow, acquire new assets, or expand their operations, digital twin models must be scalable and flexible enough to accommodate new data sources, processes, and objectives without requiring a complete overhaul. This is a significant challenge, especially for enterprise-wide deployments.
Developing a scalable digital twin architecture means designing for modularity, allowing new components or sub-twins to be added without disrupting the entire system. It also requires the underlying cloud or edge computing infrastructure to dynamically allocate resources based on demand. Ensuring flexibility means the twin’s models and algorithms can be easily updated and adapted to new operational contexts, business rules, or technological advancements. Continuous updates and maintenance are necessary to keep models relevant, accurate, and aligned with the evolving physical world. A rigid or monolithic digital twin implementation can quickly become obsolete or unwieldy, undermining its value proposition.
5.4 Ethical and Legal Considerations
The increasing sophistication and pervasive nature of digital twins, particularly in sensitive domains, necessitate careful consideration of a range of ethical and legal implications. These go beyond mere data privacy to encompass broader societal impacts.
- Data Ownership and Usage: Who owns the data generated by physical assets, especially when multiple stakeholders are involved (e.g., manufacturers, operators, third-party service providers)? What are the permissible uses of derived insights?
- Accountability for Autonomous Decisions: If a digital twin, powered by AI, makes autonomous decisions that lead to harm or failure, who is accountable? Is it the developer of the AI, the operator, or the owner of the physical asset?
- Bias in AI Models: If the data used to train the AI models within a digital twin is biased (e.g., historical operational data reflecting inefficiencies or human biases), the digital twin may perpetuate or amplify these biases, leading to suboptimal or unfair outcomes.
- Societal Impact: In contexts like smart cities, digital twins could potentially be used for extensive surveillance, raising concerns about civil liberties. The potential for job displacement due to automation driven by digital twin insights also needs ethical consideration.
Adhering to ethical standards, establishing clear legal frameworks, and ensuring transparency in the development and deployment of digital twins are crucial to build public trust and ensure responsible innovation (reuters.com).
5.5 Cost of Implementation and Maintenance
Implementing and maintaining a comprehensive digital twin solution can entail substantial financial investment. The costs are multi-faceted and include:
- Initial Setup: Procurement and deployment of IoT sensors, robust network infrastructure, high-performance computing resources (cloud or on-premise), and specialized software licenses (CAD, CAE, simulation platforms, AI/ML tools).
- Data Integration and Modeling: Significant upfront effort is required to integrate disparate data sources, cleanse data, and build accurate virtual models, which often demands expert data scientists, engineers, and domain specialists.
- Personnel and Training: A skilled workforce is essential to develop, manage, and interpret digital twins. There is a prevalent skill gap in areas like IoT engineering, AI/ML development, and data analytics, necessitating investment in training or recruitment.
- Ongoing Maintenance: Digital twins require continuous updates, calibration, and refinement as physical assets age, operations change, or new data streams become available. This involves ongoing software licenses, cloud computing costs, and personnel for monitoring and analysis.
Organizations must conduct thorough cost-benefit analyses and often adopt a phased approach, starting with smaller-scale, high-impact pilot projects to demonstrate value before full-scale enterprise adoption.
5.6 Data Quality and Volume Management
The efficacy of a digital twin is directly proportional to the quality and relevance of the data it receives. Poor data quality—due to sensor malfunctions, data transmission errors, incomplete records, or inconsistent formats—can lead to inaccurate simulations, flawed predictions, and unreliable insights.
Managing the sheer volume of data generated by thousands or millions of IoT sensors also presents a challenge. Organizations need robust data ingestion pipelines, efficient storage solutions, and intelligent data filtering mechanisms to process, analyze, and store only the most relevant information. Without effective data governance and quality assurance protocols, the digital twin risks becoming a ‘garbage in, garbage out’ system, undermining its primary purpose of providing actionable intelligence.
Many thanks to our sponsor Esdebe who helped us prepare this research report.
6. Future Prospects
The future of digital twin technology is exceptionally promising, poised for exponential growth and deeper integration across virtually every sector. Advancements in foundational technologies, coupled with evolving business needs, are set to significantly enhance the capabilities and ubiquity of digital twins, ushering in an era of unprecedented intelligence and autonomy in physical systems.
6.1 Convergence with Emerging Technologies
- Quantum Computing: While still in nascent stages, quantum computing holds the potential to revolutionize the simulation capabilities of digital twins. Its ability to process vast numbers of variables simultaneously could enable the creation of highly complex, multi-scale digital twins that model entire biological systems, global climate phenomena, or the intricate behaviors of advanced materials with unprecedented fidelity and speed. This would unlock entirely new levels of predictive power for previously intractable problems.
- Metaverse and Web3: The nascent concepts of the metaverse and Web3 are likely to profoundly influence how digital twins are experienced and interacted with. Digital twins could form the foundational ‘physics engine’ of industrial metaverses, allowing for highly realistic virtual environments where collaborators can interact with digital replicas of factories, cities, or products in a shared, immersive space. This could revolutionize remote collaboration, training, and sales. Web3’s decentralized principles might also offer new paradigms for data ownership and secure, transparent data exchange for digital twin ecosystems.
- Explainable AI (XAI): As digital twins become more reliant on complex AI models for decision-making and prediction, the demand for transparency and interpretability will grow. XAI techniques will become crucial to explain why a digital twin made a particular prediction or recommendation, fostering trust and enabling human operators to validate and refine the AI’s logic, especially in critical applications like healthcare or autonomous systems.
- Autonomous Agents and Robotics: The integration of digital twins with autonomous robots and agents will create highly intelligent cyber-physical systems. Digital twins will serve as the ‘brains’ for these autonomous entities, providing real-time environmental context, predictive capabilities, and simulation environments for learning and decision-making. This will drive advancements in self-optimizing factories, fully autonomous vehicles, and highly responsive smart infrastructure.
6.2 Expansion into New Domains
Beyond existing applications, digital twins are expected to expand into diverse new domains:
- Human Digital Twins: Beyond patient models, comprehensive ‘human digital twins’ could integrate physiological, psychological, and behavioral data to personalize health and wellness, optimize performance for athletes, or even assist in elder care, respecting strict ethical guidelines.
- Environmental and Ecological Twins: Large-scale digital twins of ecosystems, forests, or oceans could aid in climate change modeling, biodiversity conservation, pollution tracking, and natural resource management, simulating the impact of human activities and environmental shifts.
- Supply Chain Digital Twins: Moving beyond individual assets, entire global supply chains will be replicated virtually, enabling end-to-end visibility, real-time risk assessment, and dynamic optimization in response to disruptions (e.g., pandemics, geopolitical events).
6.3 Towards a ‘System of Systems’ and Interconnected Twins
The trend is moving towards not just individual digital twins of assets, but interconnected ‘systems of systems’ twins, or ‘meta-twins.’ For example, a digital twin of a smart city might comprise interconnected digital twins of its transportation network, energy grid, water management system, and individual buildings. This hierarchical and networked approach allows for comprehensive optimization at multiple scales, identifying interdependencies and cascading effects that are otherwise invisible.
6.4 Sustainability and Circular Economy
Digital twins will play a critical role in driving sustainability initiatives and facilitating the circular economy. By optimizing resource utilization, predicting equipment lifespan for repair and reuse, and tracking materials throughout their lifecycle, digital twins can help minimize waste, reduce carbon footprints, and promote more sustainable industrial practices. They can simulate the environmental impact of design choices or operational changes, guiding organizations towards greener solutions.
In essence, digital twin technology is evolving from mere virtual representations to truly intelligent, autonomous, and interconnected decision-making engines. Its integration with emerging technologies will further drive innovation and efficiency across industries, cementing its role as a fundamental pillar of the digital future (ft.com).
Many thanks to our sponsor Esdebe who helped us prepare this research report.
7. Conclusion
Digital twin technology represents a profound and transformative advancement in our collective ability to model, analyze, and optimize physical systems through dynamic, real-time virtual representations. Originating from aerospace simulations, it has evolved into an indispensable tool across a vast array of sectors, fundamentally reshaping operational paradigms and strategic decision-making processes. The comprehensive application of digital twins, from the granular optimization of manufacturing lines and the personalization of healthcare to the macroscopic management of smart cities and resilient energy grids, underscores its unparalleled versatility and tangible benefits.
The efficacy of digital twins is deeply rooted in the synergistic convergence of sophisticated technologies: the pervasive data acquisition capabilities of the Internet of Things, the robust computational power of cloud and edge computing, the predictive intelligence of Artificial Intelligence and Machine Learning, the high-fidelity simulation prowess of supercomputing, and the immersive visualization provided by advanced modeling software. These technological pillars collectively enable digital twins to bridge the critical gap between the physical and digital worlds, offering real-time insights, foresight into potential issues, and platforms for risk-free experimentation.
While the path to widespread digital twin adoption is not without its complexities—chief among them being the critical concerns of data security and privacy, the intricate challenges of integrating with legacy systems, the imperative for scalability and flexibility, and the evolving ethical and legal considerations—the overwhelming benefits far outweigh these hurdles. Digital twins demonstrably enhance decision-making by providing actionable, data-driven intelligence; they drive significant improvements in operational efficiency and cost savings through optimization; they enable proactive predictive maintenance, minimizing costly downtime; and they accelerate innovation and product development cycles by facilitating rapid virtual prototyping and testing.
Looking ahead, the future trajectory of digital twin technology is marked by even greater sophistication and pervasive integration. The ongoing convergence with frontier technologies such as quantum computing, the metaverse, and autonomous systems promises to unlock unprecedented capabilities, leading to more intelligent, self-optimizing, and interconnected cyber-physical systems. As the digital and physical realms continue to intertwine more intimately, digital twins are poised to play an increasingly central and indispensable role in various sectors, serving as a pivotal catalyst for progress, sustainability, and transformative change on a global scale.
Many thanks to our sponsor Esdebe who helped us prepare this research report.
The discussion of scalability highlights a crucial aspect. How can digital twin technology best adapt to model increasingly complex, interconnected systems, such as regional infrastructure networks, without compromising accuracy or real-time responsiveness?
That’s a great point about scalability! Addressing the complexity of interconnected systems requires innovative approaches. Perhaps federated digital twin architectures, where individual twins handle specific system components and communicate through standardized interfaces, could offer a solution for maintaining accuracy and responsiveness.
Editor: StorageTech.News
Thank you to our Sponsor Esdebe
So, with all this talk of replicating physical systems, when can I get a digital twin to attend those boring meetings for me? Think of the enhanced operational efficiencies!
That’s a fantastic idea! A digital twin for meetings could analyze discussions in real-time, summarize key points, and even identify potential action items. Think about the possibilities for improved focus and productivity. What kind of AI features would your ideal meeting-attending digital twin have?
Editor: StorageTech.News
Thank you to our Sponsor Esdebe
The report highlights the importance of data quality for digital twins. Considering the reliance on real-time data streams, what innovative methods are being developed to automatically identify and rectify anomalies or biases in the incoming data, ensuring the ongoing accuracy of the digital twin?